Elevator Ladder Logic Manual
Elevator Trainer Electrical Power & Machines 34-150. Elevator Trainer. Manual: 34-150 Ed03 012008. And programming of Programmable Logic Controllers. UDP ON “PLC CONTROLLED ELEVATOR MODEL ” In the partial fulfillment of the requirements for the award of the degree of DIPLOMA IN ENGINEERING OF.
Advanced insrumentation lab manual. 1. 1 EI 7051 ADVANCED INSTRUMENTATION LAB LAB MANUAL (Y10 Regulations) For IV /IV B.Tech (VII Semester) E. E Department of Electronics & Instrumentation Engineering VELAGAPUDI RAMAKRISHNA SIDDHARTHA ENGINEERING COLLEGE VIJAYAWADA-520 007 (AUTONOMOUS).
2 INSTRUCTIONS TO BE FOLLOWED IN MAINTAINING THE RECORD BOOK The Record should be written nearly with ink on the right hand page only. The left hand page being reserved for diagrams.
The Record should contain: 1. The number and name of the experiment 3. The aim of the experiment 4. Characteristic tables of the circuit 5. On the left hand side, circuit should be designed 6.
Index must be filled in regularly 7. You must get your record certified by the concerned staff on the every next class after completing the experiment 8. You must get your record certified by the concerned staff at the end of every semester INSTRUCTIONS TO BE FOLLOWED IN THE LABORATORY 1.
You must bring record observations notebook, while coming to the practical class without you may not be allowed to the practical. Don’t touch the equipment which is not connected with our experiment. When the apparatus is issued, you are advised to check their condition. You should not leave the laboratory without obtaining the signature of the concerned lecturer after completing the practical. Damaged caused to the property of the laboratory will be recovered. If 75% of the experiments prescribed are not completed the candidate will not be allowed for attending examinations. 3 List of Experiments 1.
Implementation of Logic gates using PLC. Implementation of timer using PLC 3. Implementation of counters using PLC 4. Level controller using PLC 5. Pressure Control using PLC 6. Motor speed control using PLC 7.
Bottle filling System using PLC 8. Temperature control using PLC 9.
Elevator controller using PLC 10. Batch process Reactor system using PLC 11. Material Handling System using PLC 12. Process control Simulator 13. Implementation of PLC programming through SCADA 14. Fan Control using PLC 15.
Reaction Vessel Control using PLC NB: A minimum of 10 (Ten) experiments have to be performed and recorded by the candidate to attain eligibility for University practical Examinations. 4 PLC INTRODUCTION A PLC is an industrial digital computer used to monitor I / P’s and depending upon their state make decision based on its program or logic to control its O/P’s to automatic a machine or a process. The main difference from other computers is that PLC’s are protected from savior conditions (such as dust, moisture, heat, cold) and has that facility for extensive I/O arrangements. These I/P arrangements directly connect the PLC to sensor and actuators. On the actuator side PLC’s operate electric motors, magnetic relays solenoids or analog O/P’s ADVANTAGES: 1.
Rugged and designed to with stand vibrators temperature humidity and noise. Easily programmed and have an easily understood programming language 3.
Audi offers America 'the only manual transmission sedan with all-wheel drive capability' in the premium segment for 2017. Download Manual: 2017 Audi A4 / S4 — Owner's Manual. Posted on 17 Mar, 2017 Model: 2017 Audi A4 / S4 Pages: 386. File size: 96 MB. Download Manual. 2017 Audi A4 / S4 — Owner's Manual. Posted on 17 Mar, 2017 Model: 2017 Audi A4 / S4 Pages: 386 File size: 96 MB. 2008 Audi A4 Avant; 2008 Audi A8 / S8. 2017 audi s4.
Have interfacing for I/P’s and O/P’s already inside the controller DISADVANTAGES: 1. Difficulty with change or replacement 2.
When a problem occurs holdup time is in definite usually APPLICATIONS: 1. In any automated system like steel plant, paper industry, COCO – COLA Industry PLC controller is usually the central part of the process system. To run more complex process, It is possible to connect or PLC controller to a control computer ARCHITECTURE OF PLC: 1. CPU: - The CPU accepts I / P data from various sensing devices, executes the stored user program from memory and sends appropriate O/P command to controlled devices. In small PLC, the processor solid state memory I / P modules and power supply are housed in a single compack unit.
The programming devices usually handling unit, a key pad and LCD display are connected to the main unit with a cable. In large PLC’s the processor and memory are in one unit. The power supply is second unit and I/P interface in additional units. The programming devices in general personal computer are connected to the main with RS232 cable serial data standard.
The Microprocessor or microcontroller is a part of PLC, CPU that receives analyses the process and sends data. The memory unit contains RAM, ROM, the fixed operating program and RAM contains the user program which is writing the ladder diagram language. The I/P system forms the interface by which field devices are connected to the controller. The I/P module converts signals from the process device (12V, 24V, 120V AC or DC) in to logic signals (5V DC) that can be used by the controller.
Elevator Ladder Logic Manual (890 Use 146 00)
The O/P module converts logic signals (5V DC) in to field level signals (12V, 24V, 120V AC or DC) to power device. Programming device: - The programming device or PC is used to enter the desired program in to the memory of PLC processor.
This program is entered using ladder logic. The program determines the sequence of operation and ultimate control by process loops TYPES OF PLC: - Name PLC – IC 200NDD101 → Versa max NANO PLC has no.
Of I/P’s 6, 24V DC I/P switches → Addresses from 1i to 6i and 4, 24V DC LED O/P’s (address 1Q to 4q) → PLC software: versa pro2.02 About the software: The software used in NANO PLC’s when designing a ladder logic diagram is versa pro 2.02.The software has been designed by GE FANUC. This is a very user friendly program when compared to the other programs.

The program has been designed to suit the operating system environment The block diagram of PLC is shown in figure 1: PROGRAMMING LANGUAGES: - The 2 most common language structures are 1) Ladder diagram language 2) Boolean language In laboratory we mostly prefer to use only ladder diagram language The ladder diagram language is basically a symbolic set of instruction used to create the controller program. These ladder instructions are arranged to obtain the desired control logic.i.e, to be entered in to the memory of the PLC. The main Symbols that are used in PLC programming are. 6 Experiment No:1 IMPLEMENTATION OF – LOGIC GATES USING LADDER PROGRAMMING Write the ladder language code for the logic gates with the help of PLC AIM: To realize the logic gates using ladder programming Procedure: - 1.
Interface PC to PLC through Rs – 232 cables 2. Go to versa pro 2.02 Icon 3. Open “FILE” go to “new folder” fill the details and click finish 4. Go to “Hard ware configuration” and replace module 5. Enter the symbols on to file using symbol on menu bar 6. Given I/P, O/P address 7. Go to PLC click connect 8.
After connecting go to PLC clear it and select all 9. After clearing go to PLC store it 10 Go to PLC go to Run 11. Thus checkout using PLC and realize respective truth tables Result: -logic gate using ladder language are realized using PLC and their truth table are verified REVIEW QUESTIONS: - 1. What are the different symbols for building ladder diagram? Draw the logic gates for AND,OR,NAND, NOR, NOT,EX – OR,EX – NOR 3. What is the software used for realizing logic gates? Explain the Boolean expression Z= XY + XY Applications: 1.
Security Systems 2. Industrial applications 3. Petroleum collection & distribution. 7. 8 Experiment No:2 IMPLEMENTATION OF TIMERS USING PLC AIM: - Design & verify the operation of timers & counters using PLC ladder language THEORY: - A timer is simply a control that waits to turn ON or turn OFF the O/P after receiving an ‘ON’ or’ OFF’ signal from the I/P.
Elevator Ladder Logic Manual Pdf
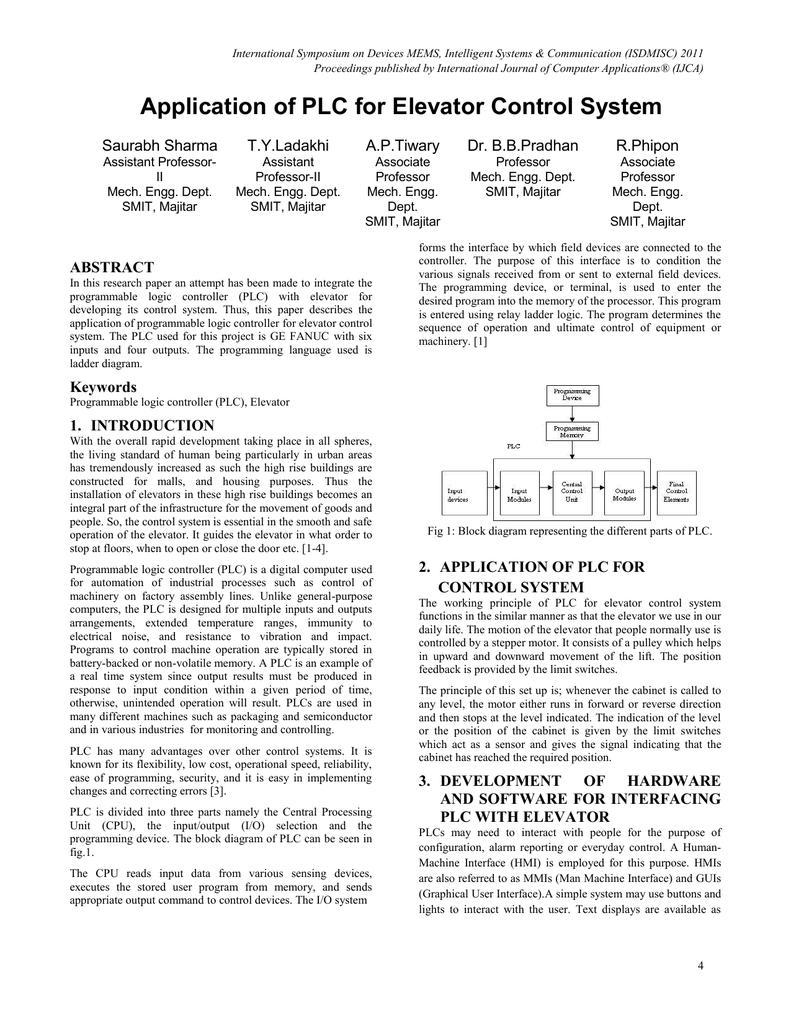
Times are basically 3 types. ON DELAY TIMER: This timer wait a specific amount of time then turns ON an O/P. The ON delay timer (TMR) increments while it receiver flow and resets to zero when flow stops. Time may be counted in tenth of a sec, Hundredth of a sec or Thousandth of a sec the range is 0 to + 327767 time units. The state of this timer is retentive on power failure, no automatic initialization occurs at power up. When the current value equals or exceeds the present value (PV) the function begins passing power flow to the right. Timer continues accumulating time to the right.
The timer continues accumulating time until the maximum value is reached. When the enabling parameter transitions from ON to OFF, The timer stops. Accumulating time & current value is reset to zero OFF DELAY TIMER: This timer takes turn on an O/P and keeps that O/P ‘ON’ until specific amount of time has passed then turns it OFF. When programming a timer instruction the programmer must specify the timer address (one of the 256 internal resistor of PLC R0 to R255). Time base (1B) and the preset value (PV).The time base value is an internal that the timer is going to use these values. Can be said to 0.1sec,0.01sec,0.001sec 0.1sec → 1/10 timer 0.01sec → 1/100 timer 0.001sec → 1/1000 timer The present value specifies how many intervals a timer should count before the timing is complete. Also known as done.
Timer selling time or delay time equals its present value multiplied by the time base. Delay time = PV X TB A timer is done when its accumulator values reaches its preset value. 9 When ‘ON’ delay timer is enabled, when its ladder rung is true An ‘OFF’ Delay timer is enabled.
When its ladder rung is false When ON or OFF delay timer is timing its rung condition change will cause the timer to stop and its accumulated value to be reset to ‘Zero’ RETENTIVE TIMER: - A retentive timer was like an on delay timer with one difference.That is when its Run conduction changes from the true to false the timer. Simply stops timing but its accumulated value is not reset to zero. When its rung condition goes false to drew. The off delay timer increments while power flow is OFF and resets to zero when power flow is ON. Time may be counted in 10ths (0.1), 100ths (0.01) or 1000ths (0.001) of a sec. The range is 0 to + 32767 time units. The state of this timer is retentive on power failure, no automatic initialization occurs at power up.
When the current value equals or exceeds the present value (PV) the function stops passing power flow to the right. The timer continues accumulating time to the right. The timer continues accumulating time until the maximum value is reached. When the enabling parameters transitions from ON to OFF, the timer stops.